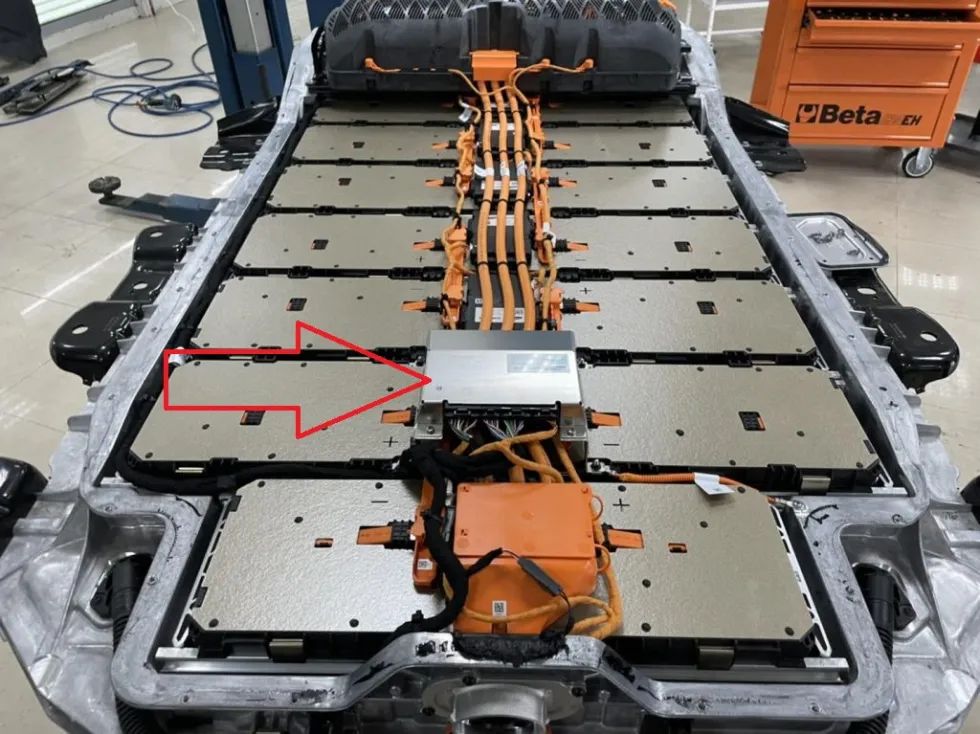
Ever wondered why sales of EU-manufactured EVs are declining in Europe while global EV sales, particularly in China and the U.S., are booming? It’s because these vehicles are complex and unreliable designed to push you back to diesel! Across these three articles, it should be clear that STELLANTIS produces and sells vehicles that systematically make ownership an ordeal. You’re forced to replace entire drivetrains for minor faults, and even minor software errors can mean replacing the entire battery due to non-resettable deactivation codes that OBD tools cannot clear. To add insult to injury, warranties are often denied for absurd reasons, like not having the first service receipt stamped or missing a wiper blade change.
STELLANTIS has done the unthinkable by tying the general warranty of the vehicle to the warranty of the drivetrain, ensuring that any failure places you at the mercy of authorized service centers that might refuse to honor warranties over technicalities hidden in the fine print. This makes owning a STELLANTIS EV an ongoing source of stress, from charging to servicing. Standard service shops shy away from touching these cars for fear of damage. Specialized service centers are few and far between across Europe, while authorized centers often resort to replacing entire batteries or drivetrains for every issue. The ownership experience of a STELLANTIS EV or PHEV becomes agonizing, especially after the warranty expires, and aftermarket servicing is even more torturous.
One of the most peculiar and legally questionable reasons for warranty refusal, which conflicts with EU single market regulations, is Fiat’s policy of rejecting warranty claims if the vehicle is ‘imported.’ This practice, seen in certain authorized service centers, undermines the principle of free movement of goods within the EU. According to EU laws, such policies are not supposed to discriminate against vehicles bought in other member states, as all consumers should be entitled to the same level of service and warranty coverage regardless of the vehicle’s country of purchase.
This approach not only challenges the EU directive aimed at ensuring non-discriminatory practices in the automotive industry but also raises concerns among consumers and consumer protection bodies. If manufacturers or service providers deny warranty claims based solely on the origin of the vehicle within the EU, they may be acting against the essence of the single market, which guarantees that goods legally sold in any EU country are entitled to move freely and receive equal treatment across borders.
Case in point: this is the 14th 2022 Fiat 500e we have serviced for the same problem—battery failure with warranty denied at only 10,000 km. The service center demanded the owner pay €13,000 for a new battery. The nightmare begins with Fiat’s so-called SGW (Security Gateway) system, which prevents anyone but authorized service centers from clearing errors via OBD. First, Fiat must unlock the port for me to access and clear errors or use special functions. This absurd system seems designed to prevent anyone but authorized services from repairing the vehicle, supposedly to prevent theft. However, when repairs are this expensive, it would have been better to leave the system unlocked—it’s cheaper for the owner to have the car stolen and buy a used one!
Unlocking SGW involves navigating through a maze of redirects and approvals to get Aftermarket authorization. We waited two months on Fiat’s site and paid over €200 for multiple accounts. We also had to order a MICROPOD II OBD tool that’s impossible to find. The FCA MDP tool from Maverick UK costs €3,000. We tried Autel, submitted the SGW Auth request, and have been waiting for two months—a waste of money. For one Fiat repair, we needed the circuit diagram and SGW access just to clear a HVIL fault. Two months of waiting, and Fiat’s account was still unresolved.
Three days ago, we accessed Fiat eLearn, found the pinout, and confirmed the HVIL issue was in the battery, not the car itself. However, the fault was neither in the battery nor the BMS, but a software problem. After 100 work hours, 20 battery removals, and EEPROM modifications, the car no longer had the active fault. But we still had to deal with SGW. We contacted a remote technician (an American of Russian descent) who used his Fiat SGW account through my Xiaomi Pad Launch5 to unlock it. Finally, we cleared the errors, and the car showed “READY” status. Another car had a “Pack B deterioration” error that locked a DTC.
The fact that it takes this much effort to fix an issue that should be covered by warranty is proof of how unreliable and unsustainable these overcomplicated, expensive systems are. And none of these cars have more than 20,000 km on them. In 2-3 years, when warranties expire, Europe will face a massive problem: a surge of broken EVs that no service center can handle due to manufacturer-imposed restrictions.
STELLANTIS also imposes exorbitant parts costs. The Continental electric motor used across their models costs €14,000 and can’t be purchased separately from the inverter. The OBC is priced at €3,800 in the catalog. There is no straightforward protocol to reprogram a used inverter, making repair unsustainable and generating unnecessary waste. Replacing an inverter or motor requires disassembling the entire front end. The system is so poorly designed that the process is excessively complex—unlike BMW, Audi, and Tesla, which offer much simpler access.
Although the Fiat 500e has its issues, I can’t say it’s a bad car. On the contrary, it’s one of the best small European electric cars. The battery problem is solvable, but we choose not to address it because it is the manufacturer’s responsibility to fix such defects. The Fiat 500e is not something to avoid, but the risk of a battery fault appearing for unknown reasons is always present. Personally, it’s one of my favorite EVs, far better than the Smart 453 or eUp. But this is explanation what Fiat closed factory and why sales are going down… customers do not believe EU manufacturers with those EV products, and they are completely right.
Our recommendations to manufacturers:
- Remove the policy tying general vehicle warranties to drivetrain warranties.
- Design drivetrains for easy disassembly – programming – repurposing.
- Make drivetrains modular and easy to replace.
- Electric motors should not cost €14,000.
- BMS, wiring, and other battery components must be available for purchase.
- Permanently eliminate the SGW, and send engineers to prison.
- Simplify the EPC catalog, documentation access, and diagnostic tools at reasonable prices (ask Tesla how).
- Simplify software updates, resetting, and programming of used units; allow public access to engineering diagnostics.
- Publicly release all .dbc protocol files.
Recommendations for owners:
- Support manufacturers that prioritize sustainable and reliable systems.
- We don’t work on DS, Citroen, Peugeot, or Opel—permanently.
ERROR CODES: P0EDD, P0A0A,











